How To Make Decorative Burnt Wood
By Matt Weber
Make Decorative Wood Pieces using Shou Sugi Ban inspired Charring Techniques
"Shou Sugi Ban" is a centuries-old Japanese method of preserving Japanese cedar siding by charring it. This wood-burning technique is now growing in popularity amidst homeowners in the U.Southward. and Canada for its decorative appeal.
The process involves charring the wood surface with exposed flame from a propane torch, then cooling it, cleaning information technology with a wire castor, rinsing, and and then applying a stop coat. Although time-consuming, the concluding product tin have a rich, silvery finish, and the charred wood resists fire, rot, insects, and tin can last for decades. Depending on the heat and cleaning technique, a wide range of end appearances can be created with Shou Sugi Ban. This application tin be used for wood siding, accent walls, wainscoting, column/beam wraps, outdoor benches, and all sorts of creative applications.
Get Inspired
In researching this topic, the EHT staff came across the folks at Inspire Woodcraft of Sacramento, California, who accept tweaked their wood-burning techniques to achieve a diverseness of truly handsome appearances and textures for wood.
With traditional Shou Sugi Ban, which literally translates to "burnt cedar board," the wood is tied together in bundles of iii, forming a triangular chimney, which is placed on-finish over a burn down, pulling the flame upwards and charring the inside faces of the boards. The boards are then taken off the fire and cooled with water, stopping the burning process and hardening the blackened, charred surface. The cooled, black surface becomes resistant to dominicus and rain, insects, rot and fire itself.
The craftsmen at Inspire Woodcraft haven't exactly adhered to Japanese tradition, and in doing and so have created some beautiful wood finishes with creative flair.
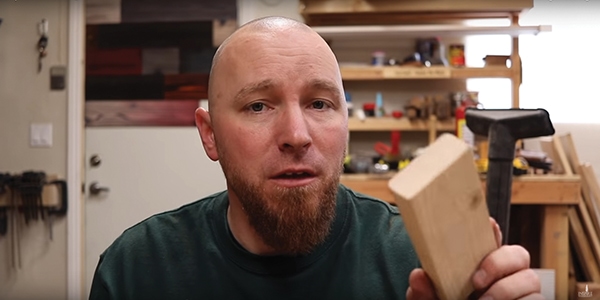
Jodee Bickell of Inspire Woodcraft explains: "Ane 24-hour interval while designing a coffee table, we had the idea of lightly burning the edges of the boards we were using, and then staining the boards one color. The theory was that information technology would give the boards a calorie-free-to-dark contrast and give an interesting visual effect. While we were right in theory, it didn't plow out exactly how we wanted. So we kept developing the process, trying to accomplish a wait nosotros were satisfied with. What nosotros soon discovered is that past fully scorching a piece of wood and so brushing abroad the loose char, the wood grain itself would stay intact and blacken, while the soft springwood in between the grain could be removed, leaving a cute, contrasting visual element not normally seen. The only logical next step in our minds was to add a colorful stain, wipe it down, and run into what happened.
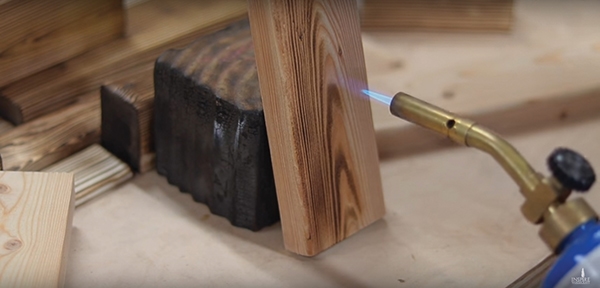
"The results that nosotros accomplished in the beginning was but that: the beginning," Bickell says. "We use dissimilar kinds of brushes, machinery, burn down techniques, milling and stain methods in our work, because each technique develops completely different results. We now have figured out how to incorporate all these different techniques to create captivating visuals for art/decor pieces and for a unique, one-of-a-kind wall covering."
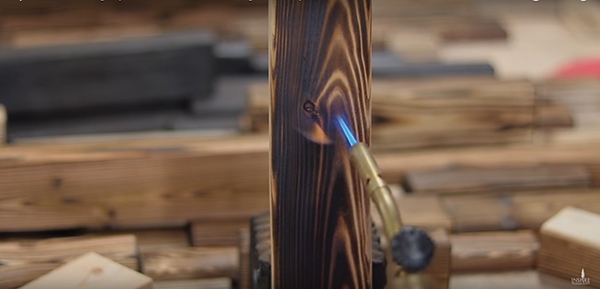
To bank check out the different burned forest finishes Bickell has achieved, EHT readers should check out the Inspire Woodcraft videos on YouTube, where he offers a detailed tutorial on the diverse phases of the process. Here's a rundown of the nuts.
Forest Selection
When selecting wood for charring, wait for construction-grade softwood lumber, such as hemlock, pine, bandbox and fir, which accept a soft grain. This is because after you burn the surface, you're going to scrape out the soft springwood between the bands of woodgrain. It's much more difficult to remove that material when working with hardwood. The soft whitewood species are also lighter in color, which essentially serves as a blank canvass for the coloration to follow. Choose forest pieces with the lightest color available.

Grain orientation is also a concern. When selecting wood, cheque the lath's end-grain for the growth rings. You desire to employ the Shou Sugi Ban technique to the exterior (bark-side) of the tree for the nearly interesting grain design.
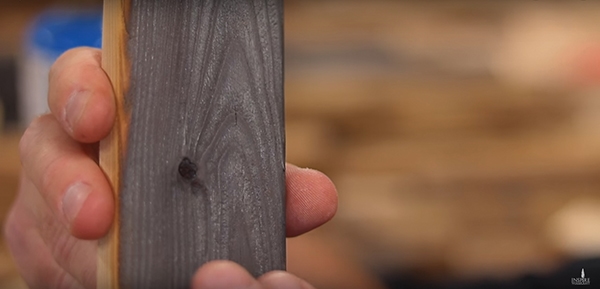
Finally, look for forest labeled "KD," which stands for kiln-dried. Forest with high moisture content won't dry out out and therefore won't work well for the charring technique.
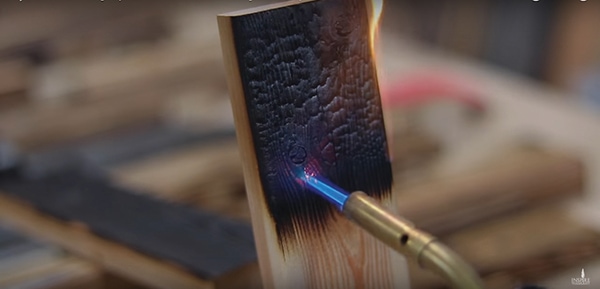
Wood Called-for Tips
For smaller projects, Bickell uses a Berzomatic torch (propane or MAPP gas) to char the wood surface. For larger projects, he uses a weed torch connected to a propane tank, but beginners should stick with a small-scale handheld Bernzomatic.
It should become without saying that you'll demand a prophylactic place to work with open flame, away from any notably flammable materials. A welding table can be used to provide a non-flammable working surface, or you can use a forest workbench if yous don't mind the likelihood of char marks.
Bickell supports the workpiece on a bench and passes the flame over the wood surface along the same direction as the woodgrain. Motion the flame in a consequent blueprint with smooth, fifty-fifty strokes to avert blotchiness every bit the wood darkens. Keep the flame the same distance from the wood throughout the process. The first pass over the entire face of the board will have some charring upshot, but information technology is essentially heating the woods in preparation for the following passes, which will char the grain and springwood. The soft springwood will burn faster and deeper than the hard grain. Notation that if y'all plan to brush out the softwood for a high-contrast upshot, and then you don't need to burn the woods to the point that it looks like firewood. If you lot plan to remove the springwood, you just need to blacken the unabridged board surface.
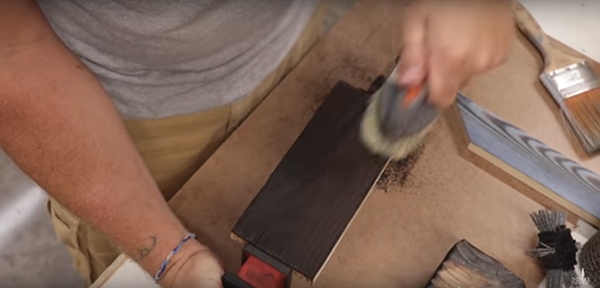
The perfect charred woods or Shou Sugi Ban-inspired finish comes down to the burn technique. This depends largely on the caste to which the surface is burned, or how long the wood is exposed to the flame.
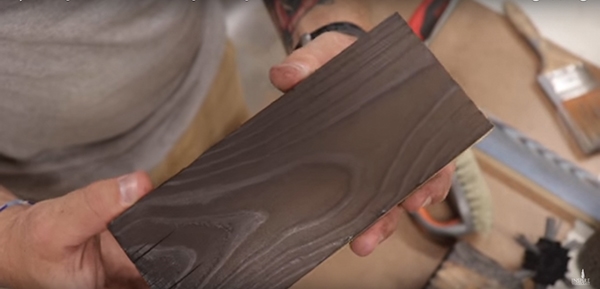
For a more than blackened end product, a unlike surface effect can be achieved past charring the wood until it won't take any more flame. This technique ultimately makes the board surface more fire-retardant only besides distorts the surface with a distinct alligator-like texture. The surface can so exist brushed to fifty-fifty out the color and and then clear-coated to finish.
Brushing the Surface
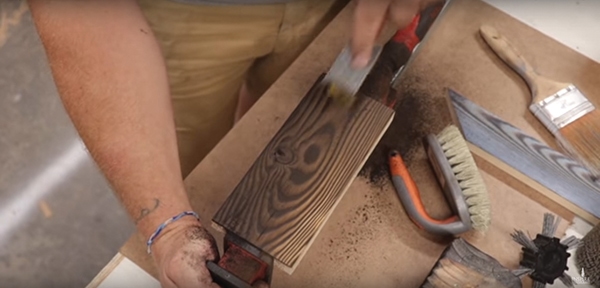
A variety of brushes can be used to different consequence. Bickell recommends a nylon utility brush for removing loose char. He uses wire brushes with beard of different stiffness (stainless steel, contumely), to vary the tooling effects left on the wood surface. He also uses a few drill-mounted castor attachments to speed up the process (specifically a Nyalox flap castor that can spin in the direction of the wood grain).
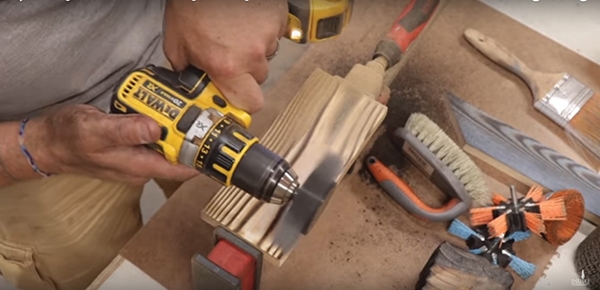
The nylon brush lonely will achieve a adequately uniform sheen. The more aggressive wire brushes will remove more char, revealing the lighter springwood beneath but leaving the dark rings of the harder grain for a higher contrast.
Stain and Finish
Afterward you've brushed and cleaned your charred wood, it tin and then be clear-coated to preserve its natural colour or be enhanced with the employ of a stain or dye. The colorants are wiped or brushed onto the wood surface, and then the excess is wiped off to get out the desired tint.
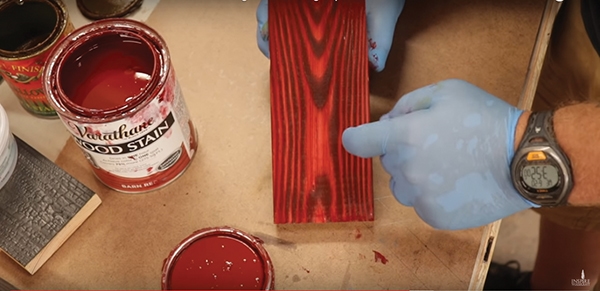
For top coats, Bickell prefers water-based products such as Polycrylic from MinWax and the thicker Enduro-Var urethane from General Finishes (fantabulous for coating a fully charred forest surface).
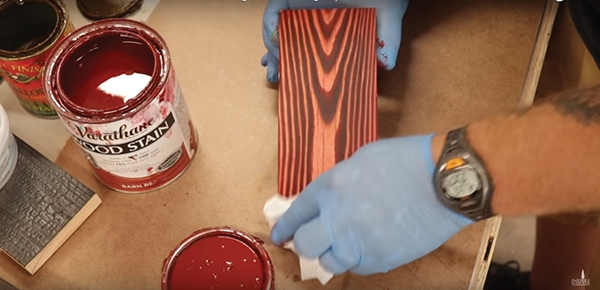
Various products and techniques can attain truly artful effects in a charred woods cease, and Bickell demonstrates these in his Inspire Woodcraft YouTube video serial, which EHT urges you to check out. He goes into detail about his personal preferences and methods of application.
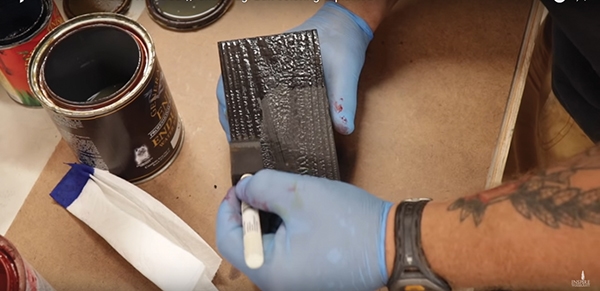
From accent walls to outdoor piece of furniture, a charred finish is an interesting design element that can give your next woodcraft projection a unique graphic symbol of its own.
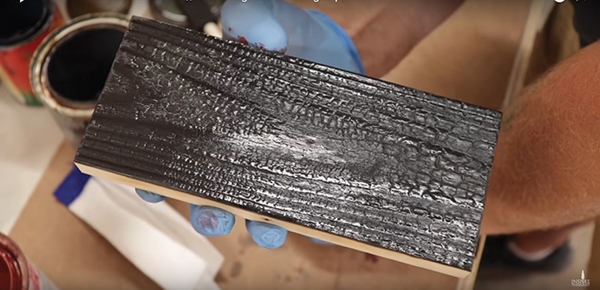
You can learn more about Shou Sugi Ban-inspired wood charring and other woodcraft techniques at world wide web.inspirewoodcraft.com.
Side Annotation 1
UFP-Edge Colorful Charred Woods Shiplap and Boards
UFP-Edge, a brand of Universal Wood Products, Inc., expands its line of Charred Wood with 7 bold and vibrant color additions: Coulee (brown), Ash (greyness), Smoke (white), Littoral (teal), Sunrise (yellow), Lava (red) and Deep Bounding main (blue). The new colors join natural Charred Wood and are available in shiplap and lath profiles at building products retailers across the U.S. Charred Forest from UFP-Edge is crafted with high-quality lumber that has been expertly burned to highlight its distinct wood-grain pattern and texture. The 1×vi-inch shiplap is easy to install on near whatsoever interior wall or ceiling. Matching i×4-in. trim and i×6 boards are perfect complements for shiplap framing, but tin can also be used for a multitude of do-information technology-yourself projects. For more information, visit www.ufpedge.com/charred-wood.
Side Annotation ii
Ignite Cladding by Thermory USA
Ignite cladding, a new production from Thermory The states, provides the await of Shou Sugi Ban with durability all the style to the core. And unlike charred wood, Ignite has no messy rest. Ignite offers the realistic expect of charred forest, without the flames. The cladding is created from thermally-modified wood using a process of oestrus and steam that enhances the wood'southward stability and lessens its weight. Ignite achieves its signature dragon scale design by embossing, brushing and tinting thermally modified Scots pino. Dissimilar modern Shou Sugi Ban, which is often created by paw with a torch, Ignite is created with a deceptively flame-free process. It is likewise available with just the brushed texture. The thermal modification gives the wood consequent rot resistance throughout the lath, a high level of dimensional stability, and a consequent appearance from batch to batch. Learn more than at www.thermoryusa.com.
Source: https://extremehowto.com/charred-wood-for-home-decor/
Posted by: perrylonaim.blogspot.com
0 Response to "How To Make Decorative Burnt Wood"
Post a Comment